PROJECTS
Scope of Work: Automation of 5 Chemical Dosing in Stock Preparationof Paper Machine.
Component Details: OBA Dosing System (Capacity 50 – 200 LPH)
DYE Dosing System (Capacity 10 – 65 LPH)
COLOR Dosing System (Capacity 500 – 2000 LPH)
CATIONIC STARCH Dosing System (Capacity 1000 – 3000 LPH)
PAC Dosing System (Capacity 25 – 110 LPH)
PLC + HMI (Touchscreen) based control panel board
Desktop (Make – DELL) with SCADA Software
The intent of the project is to optimize the control over chemical dosing parameters which would optimize the consumption levels, resulting in overall cost optimization. Each chemical dosed has a very specific role to play in the quality parameters of the paper produced; hence we have to exercise a high level of calibration and instrumentation response. The data recording function is extended to the overall project which records the chemical flow and consumption levels against the production of the paper at regular intervals.

CHEMICAL DOSING SYSTEM
The capacity of each dosing unit is ascertained as per the client requirement. The dosing systems are made of Stainless Steel grade equipped with 2 Dosing Pumps (1 Working + 1 Stand-by) along with a “STATIC MIXER” installed as per the chemical characteristic and a Twin-Filter Assembly unit. The “Digital Flow Meter” on every dosing skid displays the real time flow which can be cross checked manually.
Safety Features: All our dosing equipment`s are installed with Safety Features to protect the dosing pumps from Dry-run & against the build-up of back pressure in outlet line. We intent to provide complete safety to the dosing pump`s which are the backbone to the dosing operation. The control panel sounds an alarm with blinkers in case there is any fault in the operation and the cause of the alarm is displayed on the screen. The “Alarm Log sheet” maintains a record for rectifications.
CONTROL PANEL
CThe controls of the entire system are placed in the Control Room which houses a Desktop Computer with Control Panel Block.
The SCADA software is installed in the computer which is the primary interface for the operator.
The process control display includes:
- Level indication for every chemical service tank
- Name of Paper Grade
- Paper Machine Draw – “Ton/Hour”
- Set point of GSM as per paper quality
- Dosing flow rate of each chemical “LPH”
- Pump selection of every dosing skid (Working/Stand-by)
- Consumption levels of each chemical “gm/Ton”
- Alarm Log-sheet
- Historical Data of overall dosing parameters
In case the PRIMARY CONTROL is under maintenance, the secondary control of the entire process is available on the Control Panel block in the control room. The operator can access the functionality of the dosing system through the touchscreen HMI installed on the control panel block. The HMI displays the operational parameters of each chemical dosing system along with the tank level of respective chemicals. This provides a safety net along with easy operation to the operator.
The tertiary control panel is made available in order to serve the worst case scenario wherein the entire functioning of the dosing skid is operated through the VFD-HMI of individual dosing pumps. Safety features extended to the chemical dosing system is operational in all the above mentioned scenarios.
MORE PROJECTS

Chemical Process Automation on 3 Layer Kraft Machine
The primary reason equating the relationship of Kraft Paper Manufacturer & Chemical Efficiency at “Stock Preparation” is to showcase the dynamic yet essential bond they share. We were given the opportunity to AUTOMATE the chemical operation cycle of basic 3 chemicals used to enhance the paper quality and running ability of the paper machine – Fixing Agent (Liquid Coagulant), Retention Aid (Powder Polymer) & Micro-Particle (Liquid Polymer).
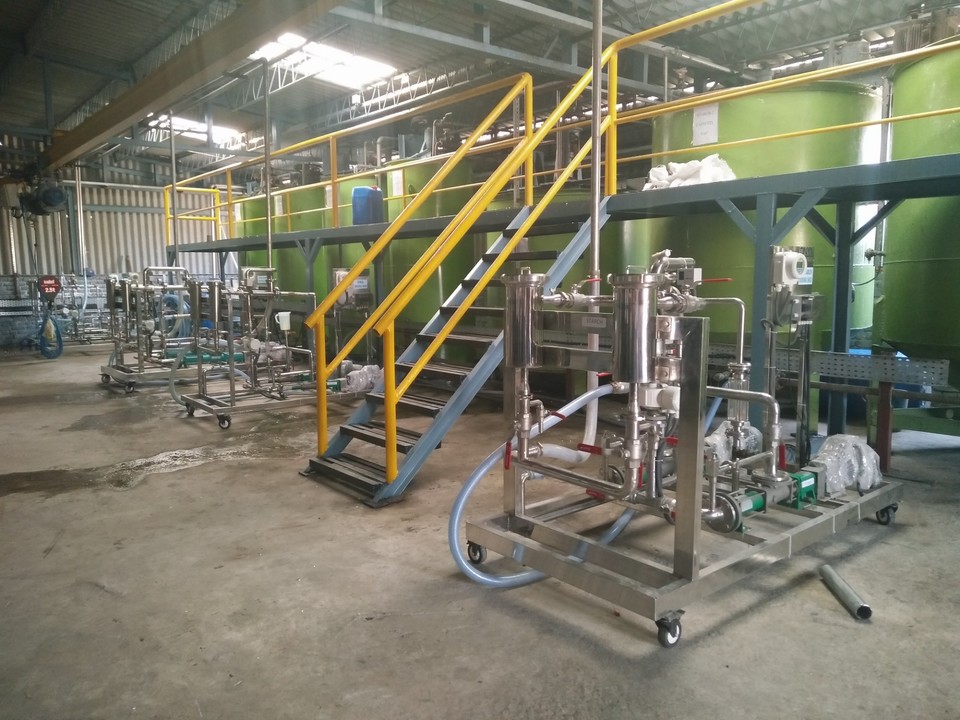
Automated Chemical Dosing for Stock Preparation - Paper Manufacturing Unit
The intent of the project is to optimize the control over chemical dosing parameters which would optimize the consumption levels, resulting in overall cost optimization. Each chemical dosed has a very specific role to play in the quality parameters of the paper produced; hence we have to exercise a high level of calibration and instrumentation response. The data recording function is extended to the overall project which records the chemical flow and consumption levels against the production of the paper at regular intervals.